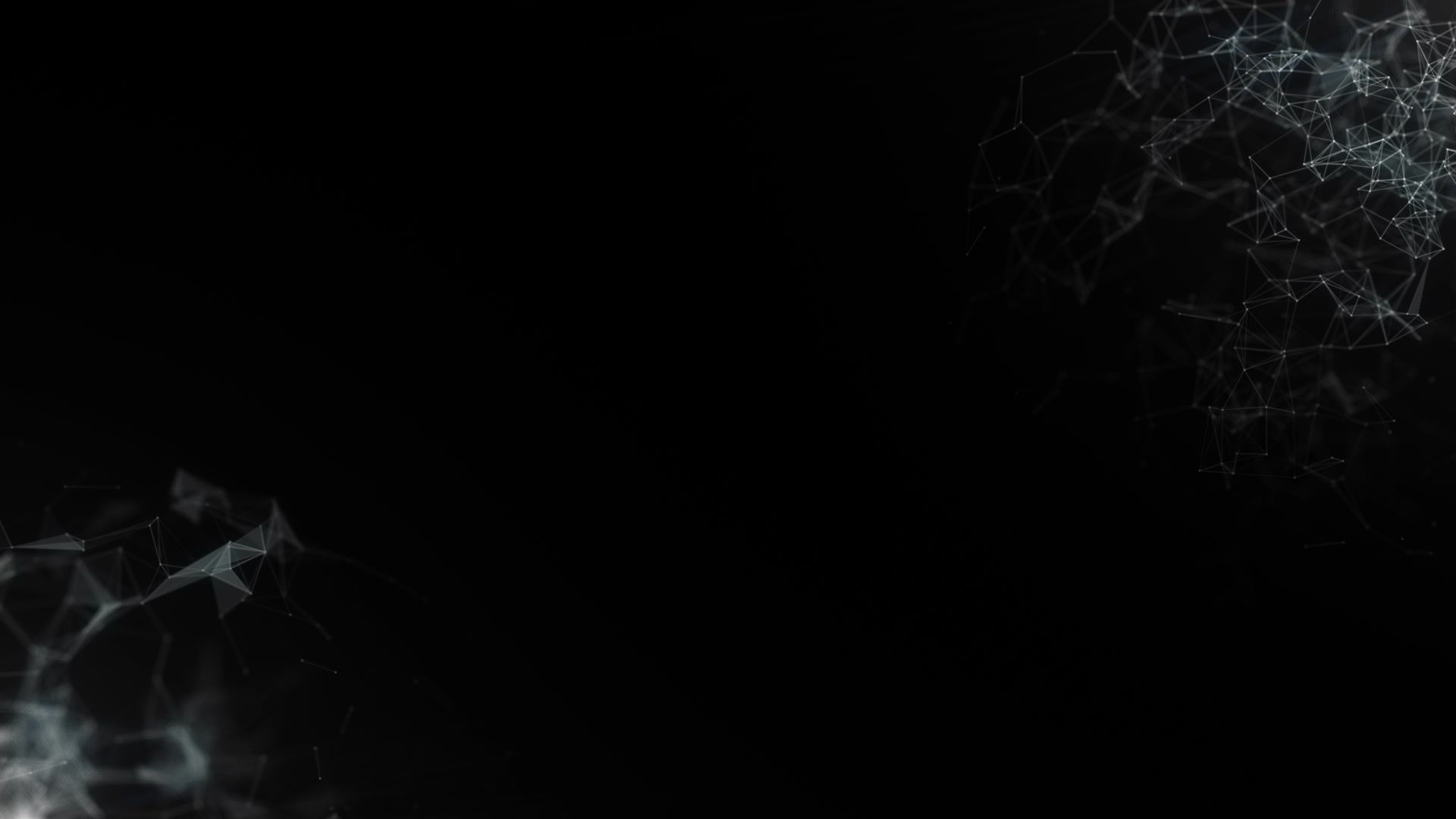
Construction


Description:
The front suspension will be built in sections. The left and right sides are mirrors of each other. The sections needed for assembly are the Lower A-arm arm, shock mounting brackets, and fasteners. The control arm and the shock mounting brackets will be manufactured. The shocks, springs and fasteners will be purchased from suppliers. The control arm will be manufactured first, followed by the brackets. First, the mounting brackets will be welded to the frame. Second, the control arm will be mounted to the frame via the mounting brackets. Third, the shock and spring will be assembled, per manufacturer instructions, and mounted to both the frame and the lower a-arm arm. In all three steps, fasteners are used to hold the sections together.
​
After manufacturing the shock mounts, it was determined that the bottom shock mounts will be bolted to the lower a-arm.
​
Manufacturing Issues:
After the design process and material selection, it was found that the section of the frame that the upper shock mount will be welded to was made from aluminum not steel, as previously thought. Because of this, the upper, along with the lower, shock mount bracket will be made from 6061 Aluminum.
During the construction of the parts, potential issues could be that drill bits are too worn down to abide by the tolerances set forth. Milling the a-arm and shock mounts could be required to be done by hand, and not through a CNC machine.
During the construction of the shock mounts it was found that using a band saw to rough cut the material on the outsides of uprights was more time efficient than using a mill to do the same operation. The slot was milled with a ½ inch end mill, instead of a ¼ inch end mill. This was done because the ½ end mill was already mounted in the milling machine. Additionally, less passes were required to make the slot.
After both the bottom and top shock mounts were made, the fit to the shock was tested. There were no problems regarding the bottom shock mounts. As for the top shock mounts, the shock body around the bottom mounting hole hit the bottom of the slot. The solution was to mill the center of the slot deeper to add clearance for the shock to rotate around the hole. This solution worked.
Once the components were being fitted, there was interference between the a-arm and the frame brackets. The solution was to use an angle grinder and a cutoff wheel to remove material from the brackets until there was no interference.
​
After construction of the top shock mounts, it was found that the frame uprights that these mounts were to be welded to were stainless steel, not aluminum as previously informed of. Therefore, the aluminum top shock mounts would not work. One avenue was to look in to if the mounts could be secured by a means other than welding. The solution was to use small flat-bar that was folded around the mount and then bolt the mount to the flat-bar, and the flat-bar to the frame upright. This proved unreliable. The final solution was to use angle steel to mate new mounts, ones that could be welded to the existing frame upright. These final mounts were made from angle steel.